Process
Electrolytic plasma polishing process
Plasma polishing process
In plasma polishing, anodically polarised metallic workpieces are placed in an electrolytic bath.
The electrolyte used in plasma polishing consists of an aqueous ammonium sulphate solution (95-98% H2O+2-5% NH3). When the workpiece is immersed in the electrolyte, discharge processes occur at the anode. This is also referred to as punctual short circuits, which lead to plasma development. The actual electrolysis processes take place in the resulting gas zone. These lead to material removal and smoothing of the surfaces.
In addition, all organic and inorganic impurities are removed with minimal loss of mass.
The surfaces are free of grease and lubricant residues. Tarnishing and discolouration are removed.
The average material removal rate is 4-10 µm / minute. The geometric shape of the workpiece is virtually retained.
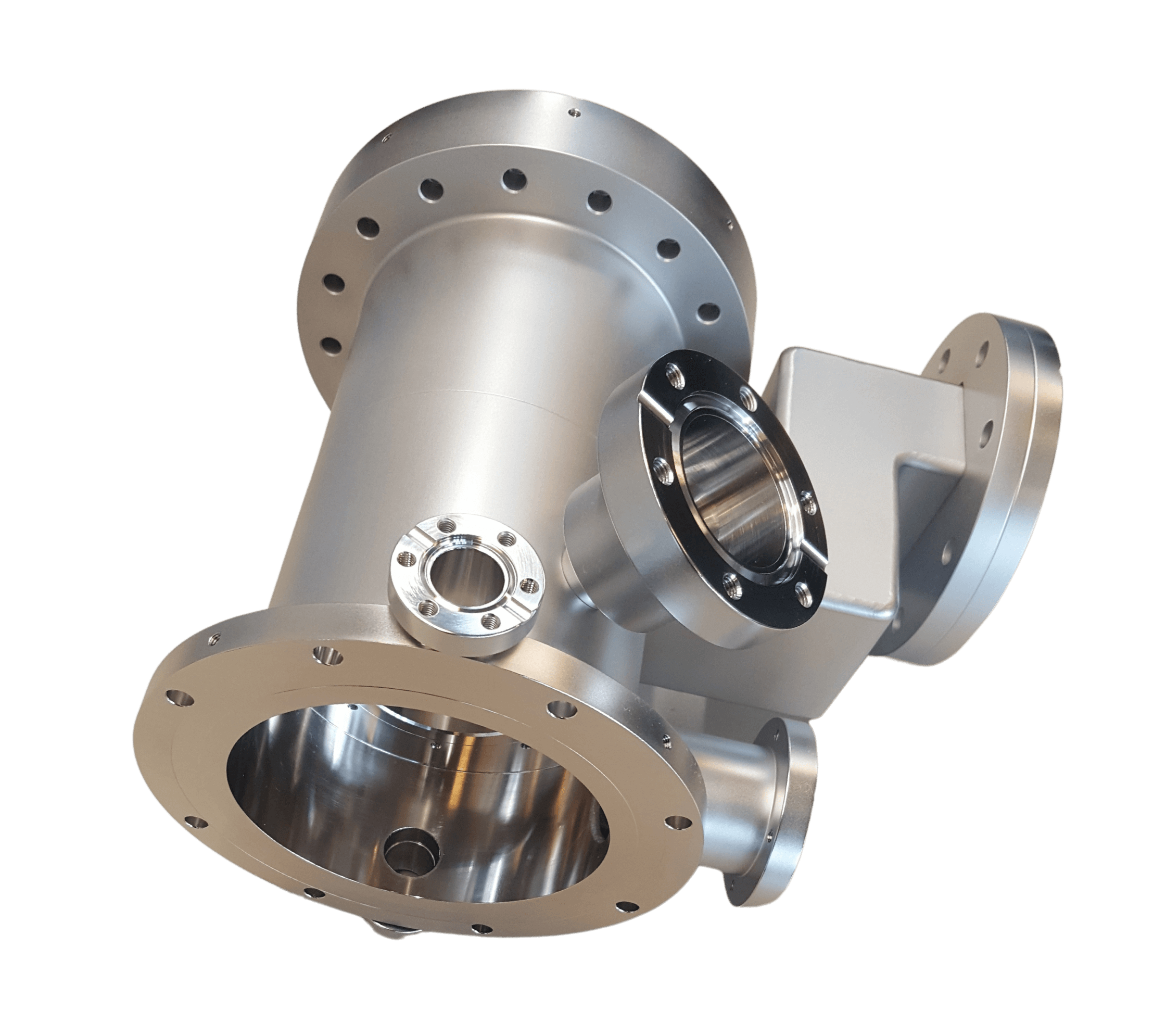
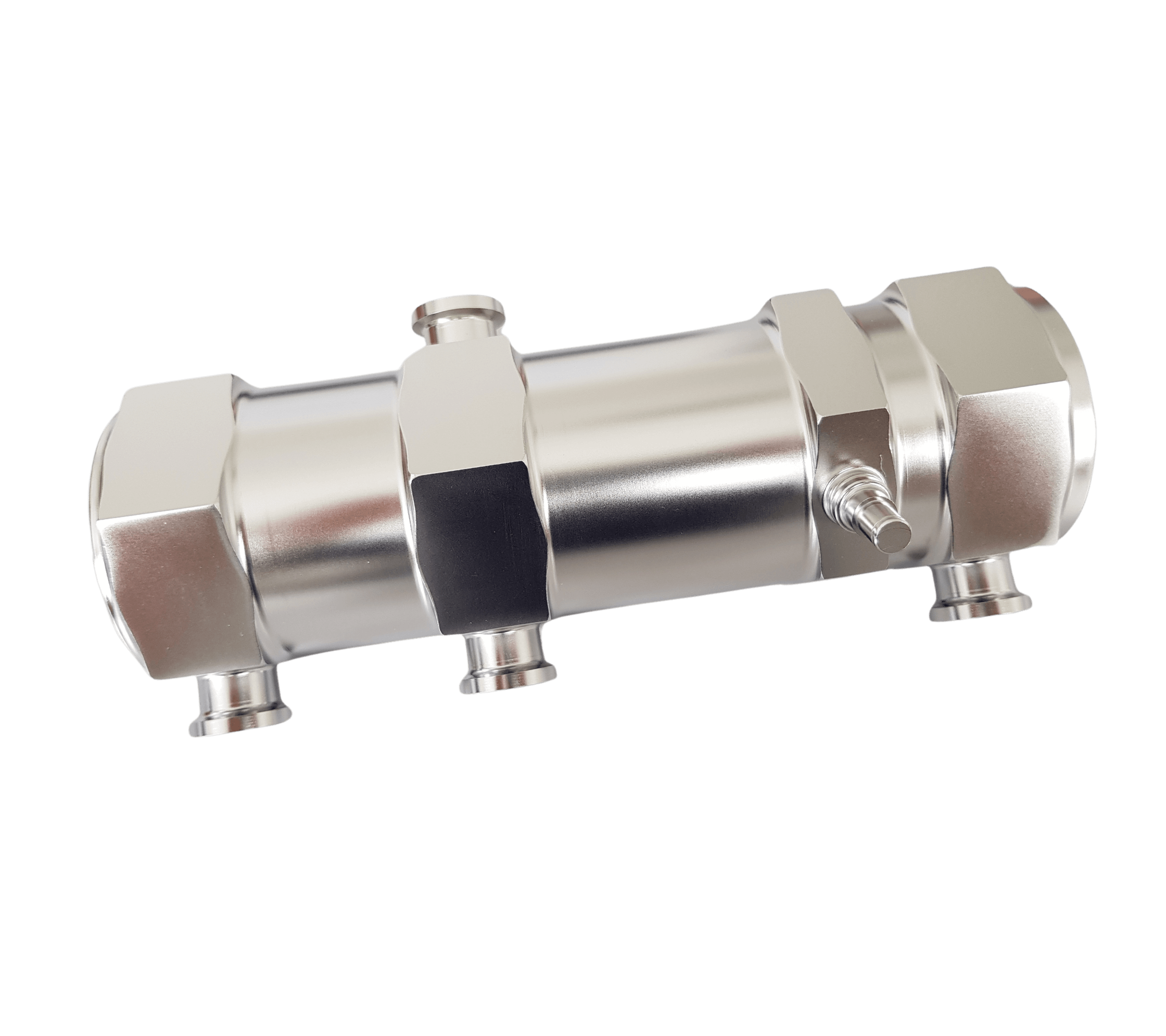
Plasma polishing process –
Differences to the electropolishing process
The first difference is the electrical bath voltage, which naturally has to be high, i.e. above 200 volts, to ignite a plasma under water. The resulting surface current density is comparable to that of electropolishing. The typical material removal rate for plasma polishing of 4-10 µm / minute is 10 to 30 times smaller than for electropolishing.
The second major difference is the electrolyte composition, which requires only small amounts of salts dissolved in water in the plasma polishing process.
The third difference is that we have so far always succeeded in finding non-toxic salt combinations with which a stable plasma and thus the special polishing effect can be generated. As plasma polishing only uses chemicals that are considered environmentally friendly, there are no problems with harmful working conditions, as is the case with conventional polishing methods. In addition, the environmental compatibility of plasma polishing is achieved through the use of non-toxic chemicals and low concentrations. The development of further material-specific electrolytes continues to take place under the aspect of environmental compatibility with regard to handling, possible material contamination and disposal.
Technology
High-gloss surfaces for functional and aesthetic applications are increasingly in demand in various sectors. To produce these, residues that can form during the manufacturing process must be removed. Polishing processes are therefore essential in order to achieve flawless surfaces.
With electrolytic plasma polishing, plasotec GmbH offers an innovative technique to fulfil these requirements. Electropolishing, a reverse galvanic process, smoothes, levels and passivates the surface of workpieces, especially those made of stainless steel.
This not only leads to visual improvements, but also increases corrosion resistance and hygiene. Electropolished surfaces reduce the development of germs and microorganisms, making them ideal for use in public areas, hospitals and the food industry.
For optimum results, the workpieces must fulfil certain requirements and be thoroughly cleaned. Electropolishing is carried out in special electrolytes and equipment to ensure the highest quality.
Discover the advantages of electrolytic plasma polishing for your applications and benefit from shiny, high-quality surfaces!
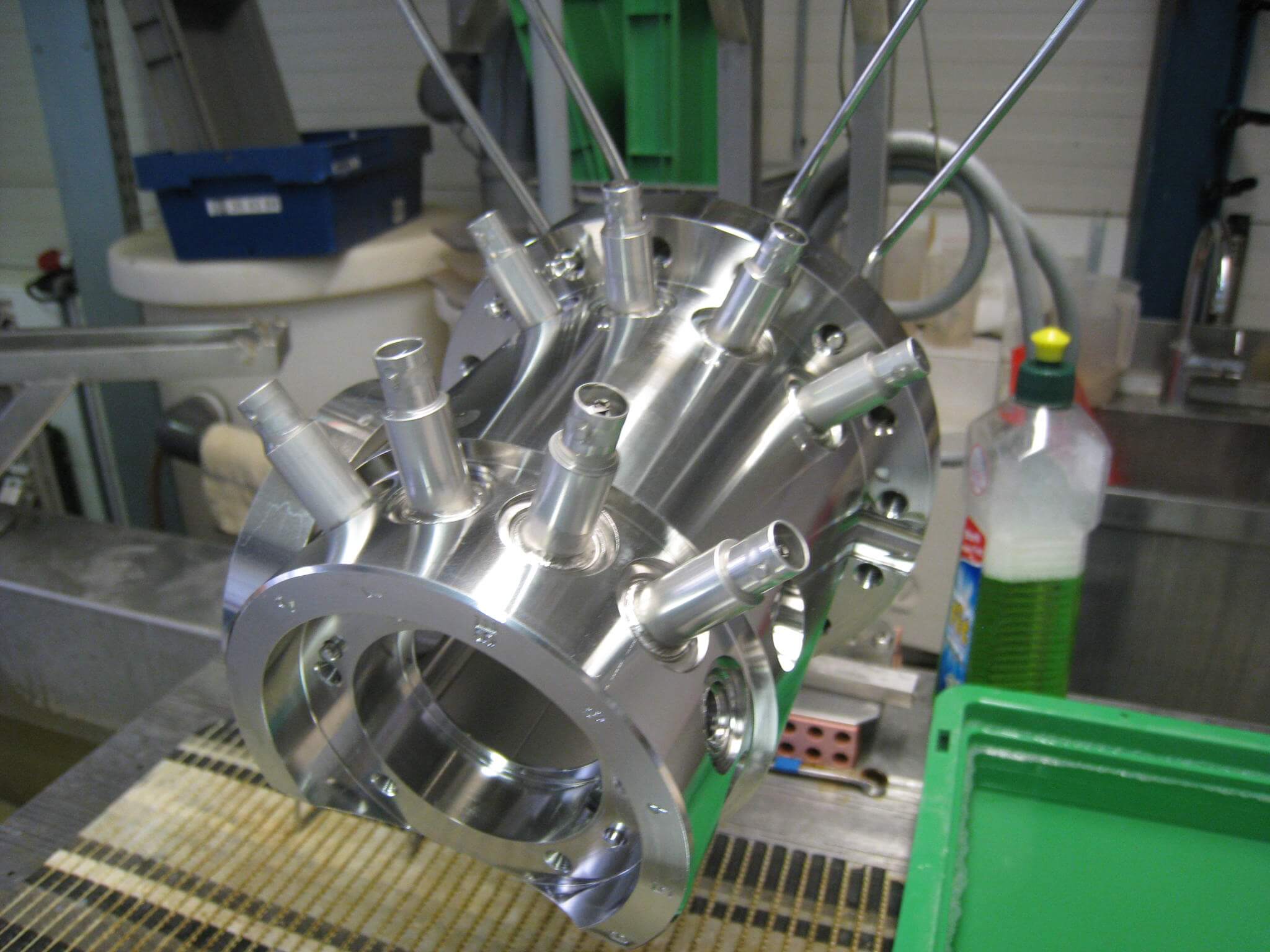
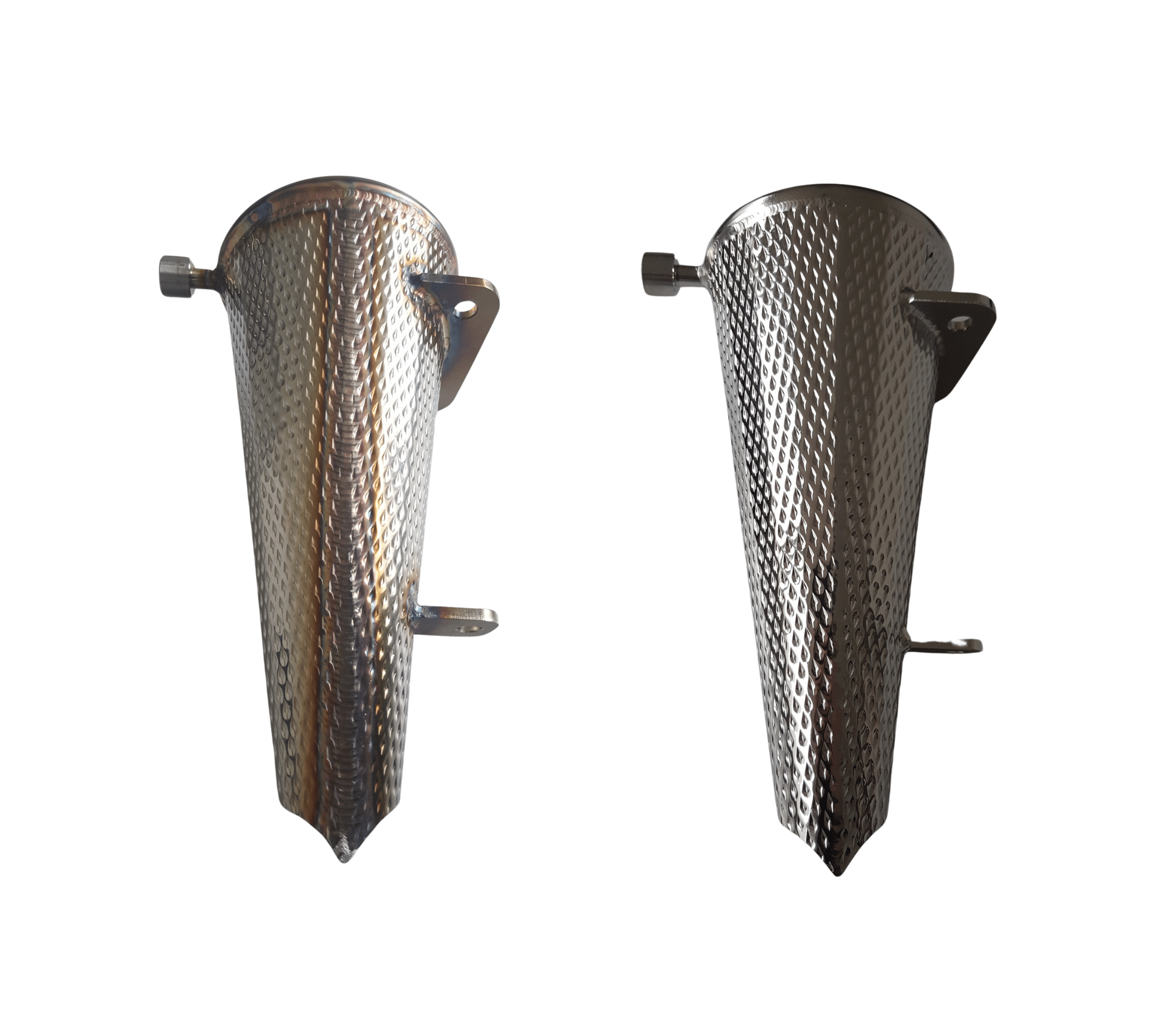
Advantages
The innovative plasma polishing process offers a whole range of advantages that make it suitable for use in a wide variety of applications. The properties of plasma polishing make this technology particularly suitable as a problem solver for polishing, cleaning and deburring metallic surfaces.
- levelling of micro-roughness (< 0,01 µm)
- minimal material removal
- processing of any contours is possible
- a previously unattainable degree of gloss can be achieved
- no pre-treatment or special cleaning of the workpieces is necessary
- use of environmentally friendly electrolytes
- no use of environmentally harmful substances and highly concentrated acids
- increased corrosion resistance of plasma-polished surfaces
- minimal thermal and mechanical stress on the surface (t < 100°C)
- no cytotoxic effects are to be expected on plasma-polished surfaces
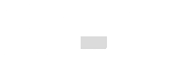